The battery market is booming and is expected to continue to do so. According to Avicienne Energy’s “Worldwide Rechargeable Battery Market 2019-2030” report, from 210 gigawatt hours (GWh) in 2005, the world market for rechargeable batteries reached 630 GWh in 2020. By 2030, Avicenne estimates that the battery market will double again, to 1,300 GWh, for a total value of $150 billion (€124 billion). Production capacity for these components is currently concentrated in Asia. In this race against the clock for batteries, Europeans are getting organized and battery factory projects are multiplying.
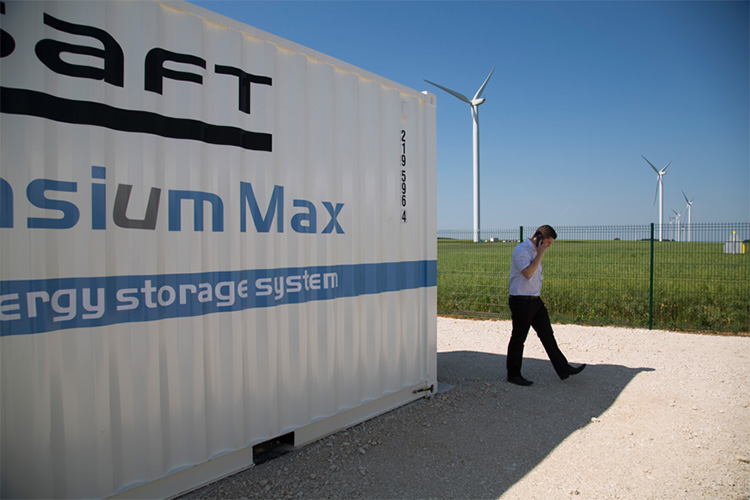
Automotive Cells Company (ACC), the joint venture created in 2020 by Stellantis (ex-PSA) and Saft Batteries, is positioning itself at the heart of the system: the cell. On a plot of land at the Stellantis site in Douvrin (Pas-de-Calais), ACC is due to commission the first 8 GWh block of its first electric vehicle battery gigafactory at the end of 2023. The Gigafactory will manufacture the electrodes, assemble and test the cells, and assemble the modules ready to be mounted on vehicles.
French battery manufacturer Verkor, supported by the European innovation and technology institute InnoEnergy, Schneider Electric, the Idec Group and Capgemini, wants to launch a 16 GWh capacity factory in 2024, with a final production target of 48 GWh. The site selected in France will be announced this summer.
While priority will be given to the automotive industry because of the volumes required, other markets will also be targeted, such as stationary energy storage to serve the flexibility of the electrical grid.
In the energy sector, Li-ion batteries are indeed used as a primary reserve for networks or to cope with the intermittency of solar and wind energy production.
In France, the stationary storage market is developing rapidly. The largest battery-based electricity storage system was built at the end of 2020 in Dunkirk (Northern France), following a call for tenders issued by the electricity transmission company RTE. The project was carried out by Omexom in collaboration with Total Solar International and battery manufacturer Saft, a Total subsidiary, which is supplying the Intensium Max 20 High Energy solution. Featuring a 25 megawatt-hour (MW/h) storage system with 25 MW of power, the project required an investment of approximately €15 million and includes 11 integrated containers, each with a capacity of 2.3 MWh, designed and manufactured at Saft’s production site in Bordeaux.
Located on the site of the former TOTAL refinery in the port of Dunkirk, the system is connected to RTE’s very high voltage (VHV) electricity transmission network. The first phase of the large-scale battery energy storage system (BESS) is operational and provides 24/7 services. The site will help regulate the frequency of the electrical network and support the network during the coldest days of winter when it is under tension. The integration of renewable energy will also be facilitated.
The aim of this project is to secure the electricity supply, regulate the frequency of the network and combat the intermittent nature of renewable energy production.
The battery industry is also developing through the growth of intelligent battery systems, both for microgrid solutions and for mobility. French manufacturer Gaussin will deliver 36 electric tractors to Côte d’Ivoire for the development of the second container terminal at the port of Abidjan. This new port aims to become a pioneer in terms of eco-responsibility. The tractors have 100% zero CO2 emissions and no noise pollution. They reduce the cost of energy consumed at the terminals by 70%. Blue Solutions’ LMP solid state batteries offer significant guarantees of reliability, autonomy and safety to meet the port’s logistical needs and should contribute to a significant reduction in its environmental footprint to obtain the “Green Terminal” label.